We receive this question often. The custom material we currently use for the reservoir has a thin film layer of polyethylene plastic laminated to a high tensile strength nylon material.
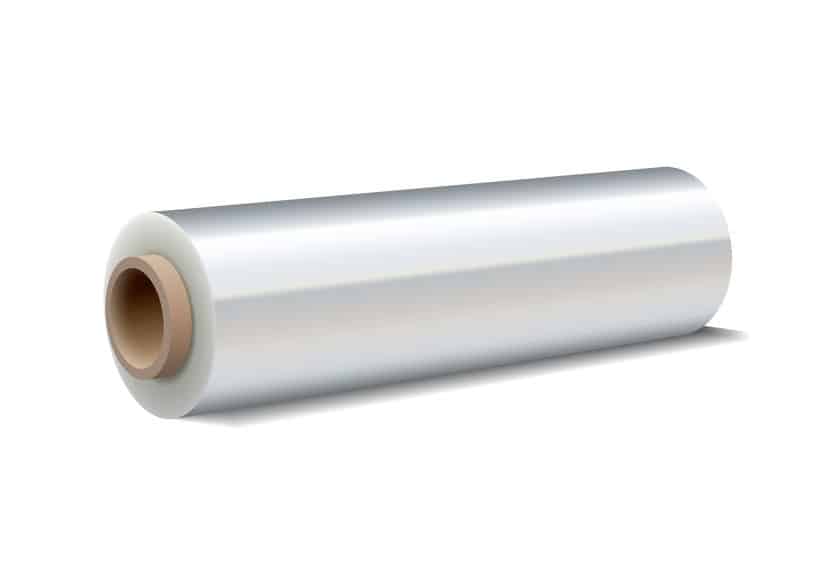
See Also:
The “air” only comes in contact with the PET thin film side of the material. PET is considered non-reactive even in high oxygen concentration environments. For practical reference, the material is the thickness of a single layer of kitchen plastic wrap.
The reservoir’s purpose is to retain oxygen. Our tests show that oxygen diffuses out over about 24 – 48 hours.
This enables users to rely on a high concentration of oxygen during training — but minimizes total plastics to only enough to retain the oxygen for a reasonable amount of time.

This just-right balance explains why LiveO2 reservoirs never have an odor. The oxygen +O2 side air just smells clean. The hypoxic ‑O2 air is warmer and naturally concentrates environmental odors because odor-causing molecules concentrate in ambient air filtrate during molecular air separation.
LiveO2 reservoirs do not tend to absorb environmental contaminants because they have minimum embodied plastic. A LiveO2 reservoir contains about 30 grams of non-fabric plastic, which is about 2 tablespoons stretched into the thinnest possible sheet.
The thin sheet minimizes the absorption capacity and prevents odor from lingering. This is why LiveO2 reservoirs smell clean even after they’ve been exposed to environmental chemicals, like smoke or cleaning agents. Reservoir chemical absorption capacity is very low due to a very small amount of embodied plastic.
Here is the sequence of reasons why LiveO2 reservoirs have no odor:
- Reservoirs use a very small amount of plastic. The reservoir has a total of about ~30 grams of PET — PET is the cleanest plastic available.
- The plastic is very thin, .5 ml to minimize capacity and quickly release gasses. The PET has stretched to a very thin .5 ml and then heat-bonded to a strong porous fabric that rapidly dissipates gasses to the environment.
- LiveO2 materials age 2 – 6 months so there is lots of time for residues to dissipate prior to customer contact.
- The PET layer is two-sided. Half of the embodied volatiles dissipate external to the reservoir.
- LiveO2 reservoirs release gasses that may accumulate inside with a quick drain zipper-port, non-sealed seams. The design enables cleaning and maintenance in case of exposure to smoke, cleaning agents, or other chemicals. Unsealed design enables gasses that may leach during storage to escape.
- Thin plastic construction minimizes absorption capacity. Odors to smoke, cleaning solutions, and other chemicals dissipate quickly, within a day, to an undetectable level, hence liveO2 reservoirs always smell clean.
- Supports Ozone Purification. LiveO3 can be used to sanitize LiveO2 reservoirs by filling the reservoir with ozone in case of chemical exposure or other contaminants.
Formal Testing of New Materials
During normal use, volatile chemicals are undetectable in LiveO2 reservoirs.
Nonetheless, Good Manufacturing Practice includes determining the maximum possible VOCs that can be released over the Lifetime of the LiveO2 reservoir.
The max Lifetime VOC Release Test
This test determines how much VOC is present in the materials when they are created. This test determines the maximum amount that may be released over the physical product lifetime.
Outgas Test
Material outgas tests are designed to test the total amount of outgas material present in a sample of new material. A sample of material, normally ~10 grams, is enclosed in a small vacuum-sealed container, normally ~100 cc, and baked at 250 C for 1 hour.
After baking, the pressure of the container is measured. The increase in gas pressure in the container approximately represents the total amount of VOC that the sample material may release over the service life of the sample.
These conditions provoke outgas tests in the range of the lowest detectable limit VOCs: <4 ug/g, <4 ppm.
Even these levels are far within acceptable safety standards and exceed safety standards for VOCs present in new homes and new cars.